Induction motor
Asynchronous motors have a passive rotor that is permanently short-circuited (squirrel-cage rotor) or temporarily short-circuited (see slip ring rotor). It can generate up to several megawatts of power and is most commonly used as a standard three-phase motor in industrial applications.
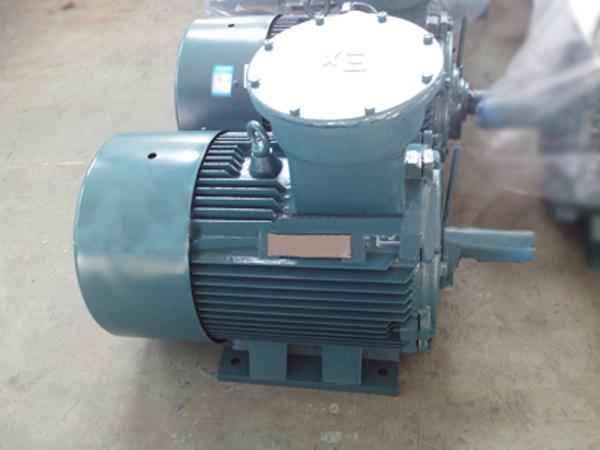
The magnetic field in an asynchronous motor is generated by the electric energy provided by the excitation current. The characteristic of asynchronous motors is slipping. The difference between the rotor speed and the speed of the rotating magnetic field of the power supply voltage depends on the load.
The rotor is a metal cage, the shafts of which are arranged in a symmetrical circle and fixed on the short-circuit ring (end ring) at both ends.
The stator consists of distributed coils that induce voltage into the bars of the rotor through a rotating magnetic field (see induction). This causes a large amount of current in the shorting bar to flow, thereby exerting a force between the rotor and the stator in the magnetic field and causing asynchronous electromagnetic interaction. Asynchronous motors suffer significant losses in the stator and rotor.
In a slip ring rotor motor, the three-phase rotor winding is connected to a variable resistor (usually used as a liquid starter) through a slip ring. This design ensures that the soft-start process will not impose an impact load on the power mains and can change the speed to a certain extent. However, it also produces a large power loss.
The rotor winding of a squirrel-cage rotor is usually composed of a single or double conductor strip, and their ends are short-circuited by a ring conductor. The design of the squirrel cage rotor is very simple and reliable, and does not require maintenance.
Dry rotor, submersible motors and wet rotor motors differ in terms of water contact.
Internal wetting external wetting
Rotor winding dry shell wet shell (submersible motor)
Dry dry dry motor (with or without water seepage protection) dry (air filled) submersible motor
Wet (wet rotor motor) dry (canned motor) wet rotor motor without seal pump, fully submersible (fluid filled) motor
Figure 2 Asynchronous motor: specify the asynchronous motor according to the wetting condition
Dry motors have different types of protection against water seepage (see Types of Protection).
The submersible motor is partially or fully immersed in the water, usually installed in a vertical position. The heat generated by the motor is directly transferred to the surrounding fluid. Its main feature is its motor housing, which is wetted from the outside (see Submersible Motor Pump). Internal immersion and immersion depth distinguish oil or air immersion immersion motors from medium immersion depth (medium submersible pumps).
The motor that was completely immersed in water was wetted by internal and external treated fluid. They are suitable for any immersion depth and are first used for drilling (see submersible drilling pumps), which is why they are small in diameter and relatively long. Fully submersible motors can be equipped with wet stator windings (including waterproof plastic insulation) or can be equipped with dry windings along with the tank (see Canned Motor Pump).
A wet rotor motor is filled with liquid, and unlike an immersion motor, its housing is not wetted from the outside. It has liquid-lubricated bearings (see sliding bearings) and forms a sealed pump set (unsealed pump) with the pump. The motor can be equipped with wet stator windings or with dry windings together with the tank, which is usually the motor of choice for circulating pumps.